Production processes in industrial companies are becoming increasingly complex. Technical cleanliness is an important parameter to prevent breakdowns or even recalls. Using the WEBER principle, we explain everything you need to know about technical cleanliness.
What you should know about technical cleanliness
Therefore be technically clean!
What technical cleanliness means
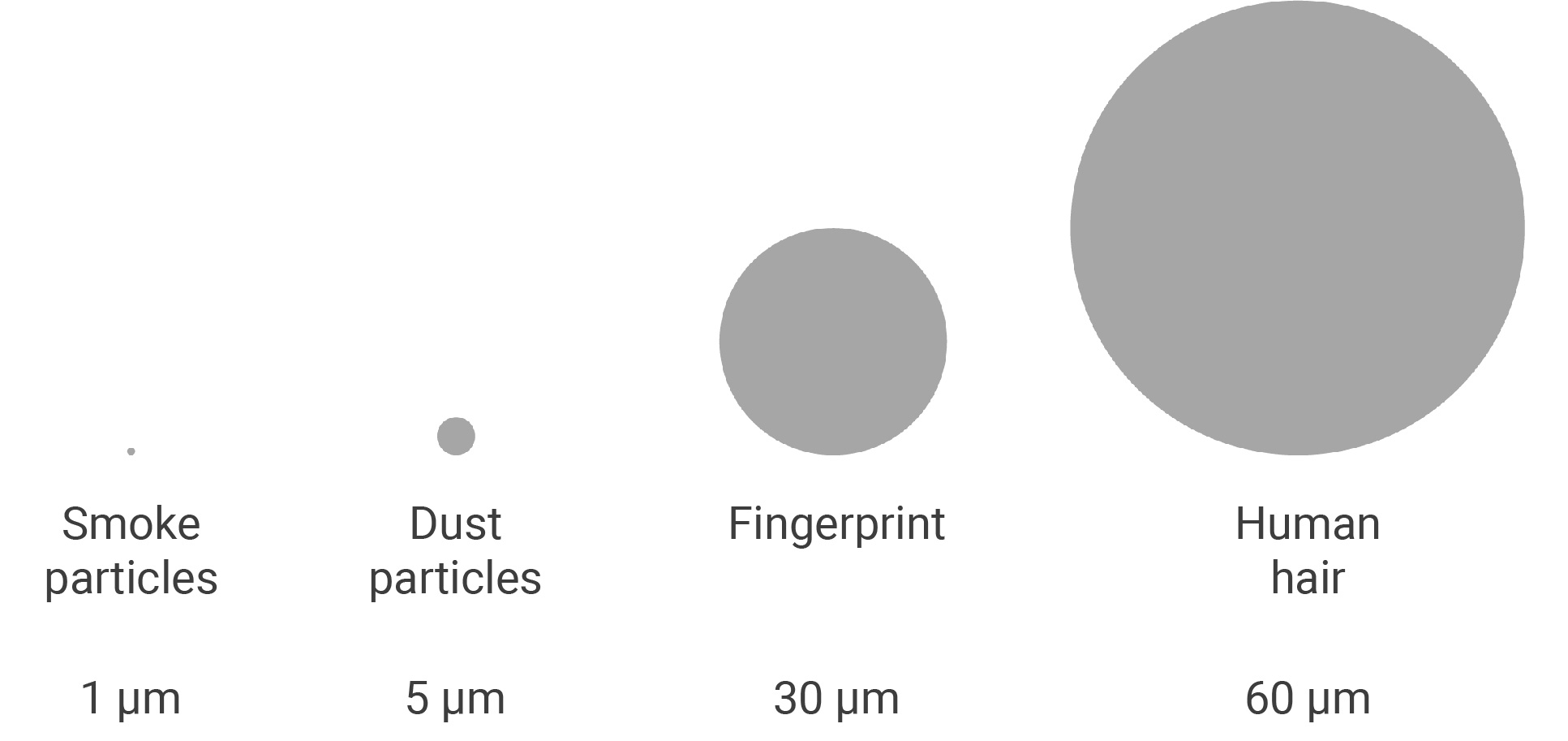
A component is “technically clean” if its level of contamination is sufficiently low. It is therefore essential to first check for unwanted contamination. The next step is to clean the surfaces of the workpiece. This technical cleaning must have a required to agreed or possible degree. It is also important to correctly define the condition of the component. In the case of production-related contamination, a distinction is made between particulate and film contamination. Possible forms of contamination can be
Particles, chemicals, oils, greases, chips, fibers, oxides, rust and scale
You can see a size comparison in the graphic. Measures taken in the field of automated assembly are aimed at particle sizes of > 5 µm. Assembly and joining processes can produce particles that are classified as functionally critical due to their metallic consistency compared to fibers from the environment. WEBER technology for technical cleanliness is specifically aimed at minimizing these particles.
Cleanliness levels
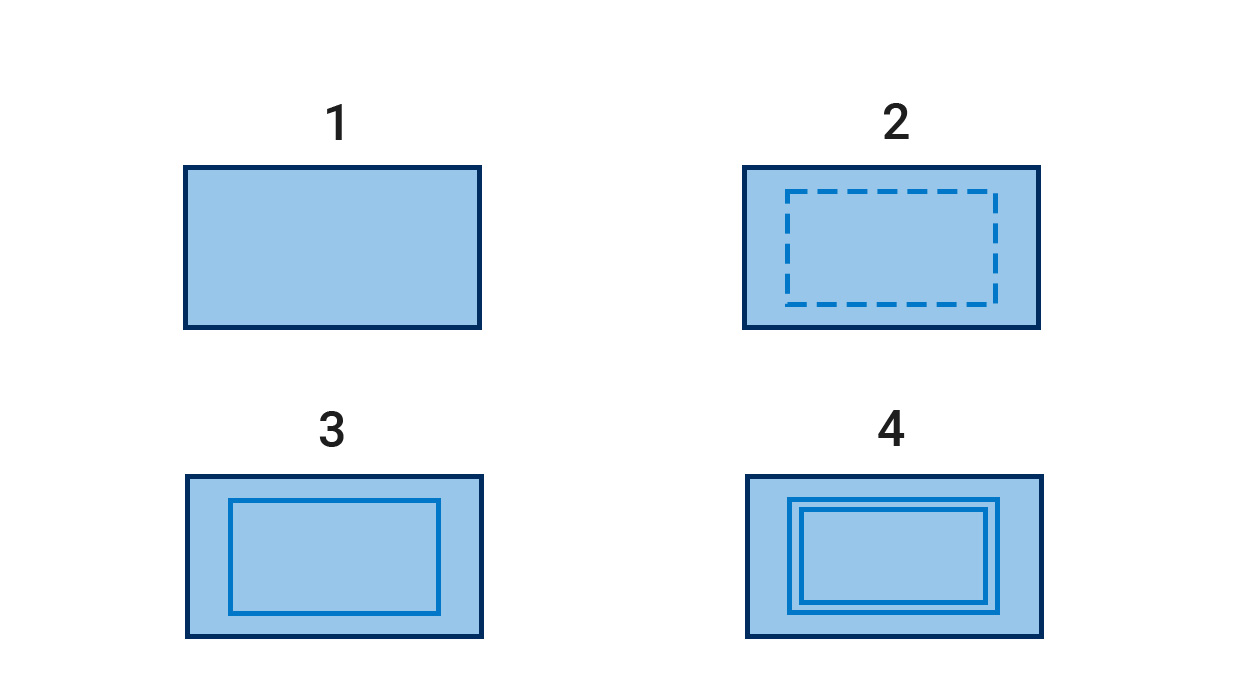
Classification of cleanliness areas:
- Non-regulated area
- Clean zone
- Cleanroom
- Cleanroom
Nicht regulierter Bereich |
Sauberzone | Sauberraum | Reinraum | |
---|---|---|---|---|
Abgrenzung gegenüber potenziell kritischen Bereichen |
– |
z. B. Bodenmarkierungen, Stellwände, Decken-Schürzen |
fest installierte bauliche Abgrenzung |
fest installierte bauliche Abgrenzung |
Sauberkeitsorientierte Regelung innerhalb des Bereichs und bezüglich Material- und Personentransfer zu angrenzenden bzw. anderen Beriechen. |
– | x | x | x |
Reinlufttechnik, die über die Raumklimatisierung hinausgeht |
– | – | (x) | x |
Ausgeprägtes “Raum-im-Raum-System” mit Schleusenkonzept |
– | – | – | x |
Klassifizierung nach VDA Band 19 Teil 2 |
Sauberkeitsstufe 0 (SaS0) |
Sauberkeitsstufe 1 (SaS1) |
Sauberkeitsstufe 2 (SaS2) |
Sauberkeitsstufe 3 (SaS3) |
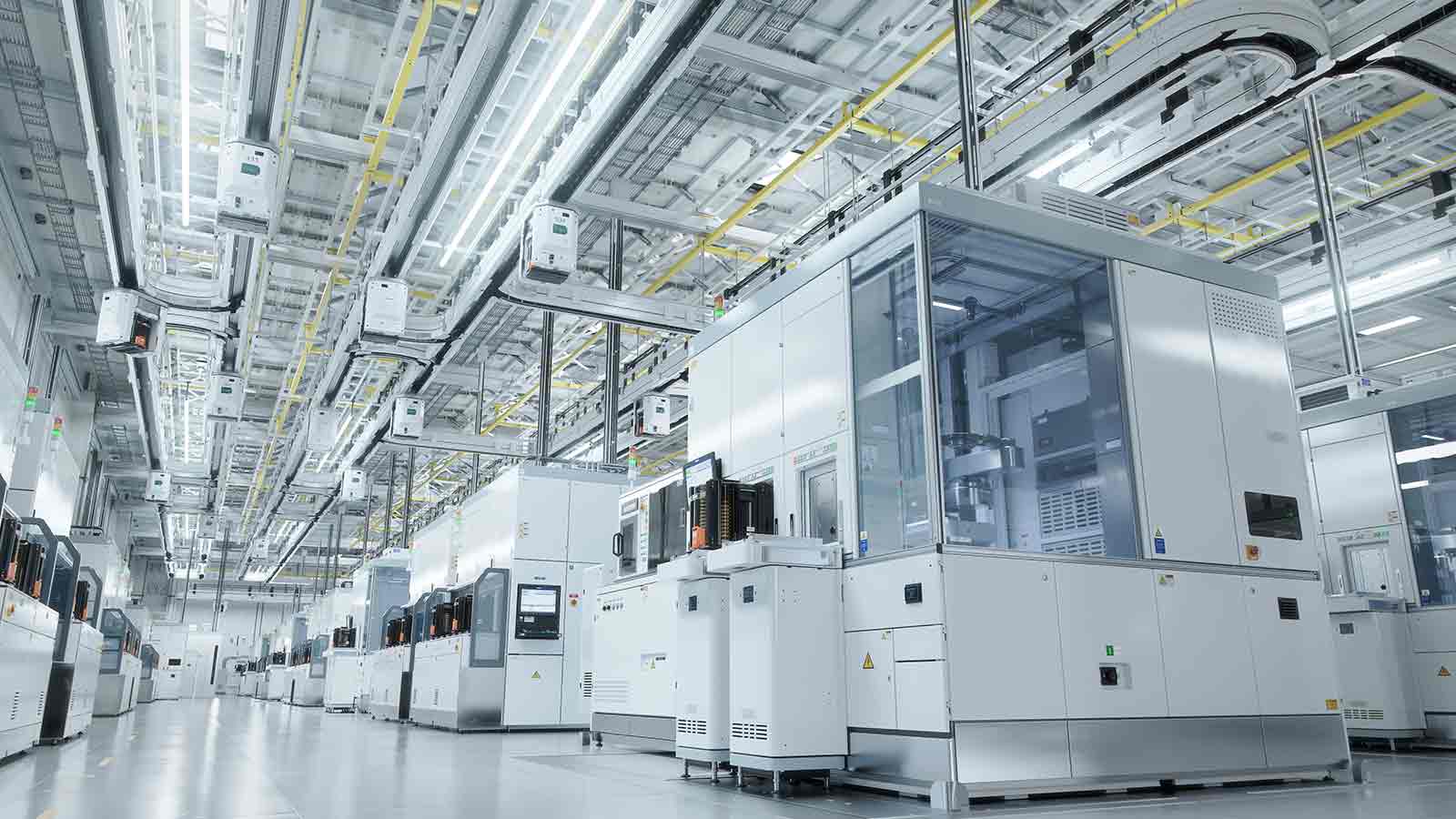
Ideally, clean production processes take place in the cleanroom. The “cleanliness through ultra-fine cleaning in the cleanroom” applies to the cleanliness condition of the screws. The following conditions must be created to meet the highest quality requirements:
- Cleanroom-like concept
- Integrated ultra-fine cleaning, anti-friction coating and packaging
- Stable process sequence
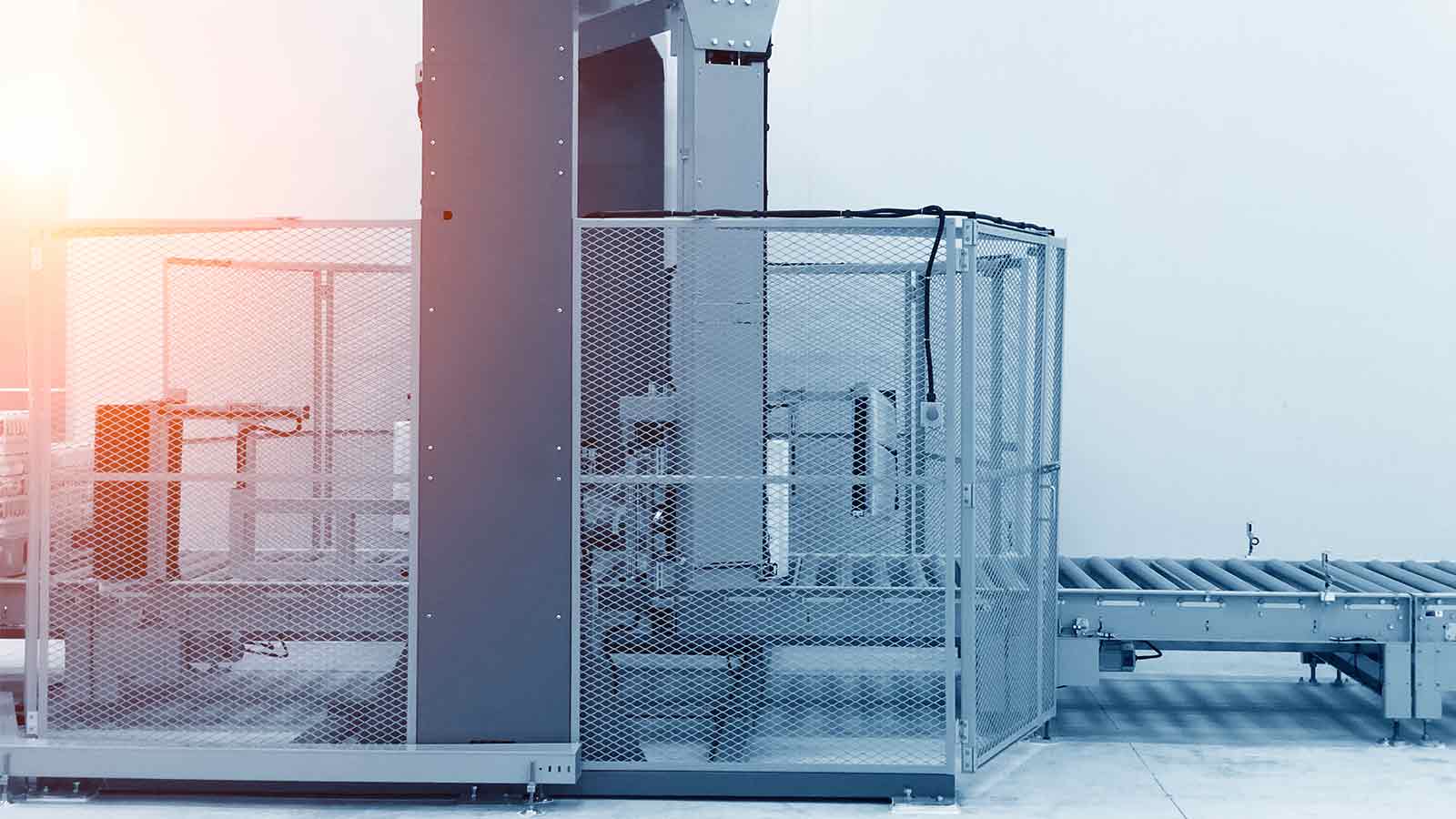
The increased cleanliness standard also applies to the transportation and handling of screws. This means:
- Position-fixing onion skin principle
- Compatible with all standard small load carriers (KLTs)
- Antistatic inner packaging
- No additional contamination of the environment
Achieving and maintaining a high level of technical cleanliness is essential in many industries as it can have a significant impact on product quality and safety as well as production efficiency and costs.
1. PRODUCT QUALITY
Contamination can have a negative impact on the performance, function or appearance of products. For example, dirt or dust particles can clog moving parts or affect electrical connections, while liquids can cause corrosion. Furthermore, it is possible that contaminants can also affect the aesthetics of products, making them less visually appealing to the consumer.
2. PRODUCT SAFETY
Contamination can even pose safety risks for product users. Metal shavings in electronic devices, for example, can pose a fire or short-circuit hazard.
3. PRODUCTION EFFICIENCY
Production problems and downtime as well as increased scrap rates and costs are also possible consequences of contamination. For example, if production equipment becomes clogged with dirt or debris, it may need to be cleaned more frequently, leading to a reduction in overall efficiency.
4. COSTS
The cost of cleaning and maintaining technical cleanliness can be considerable, especially in industries where strict standards are required. The benefits of clean assembly are demonstrated by the WEBER approach in the cleanroom for technical cleanliness. Not only are there fewer failures of functionally and safety-relevant components, but also better opportunities for component miniaturization. Thanks to improved assembly safety, there are far fewer faults caused by contaminated feed and screwdriving systems. The service life of our assembly systems is extended enormously as there is hardly any wear and tear. Improved quality means nothing other than reduced complaints and attractive cost savings. Translated with www.DeepL.com/Translator (free version)
How to achieve technical cleanliness
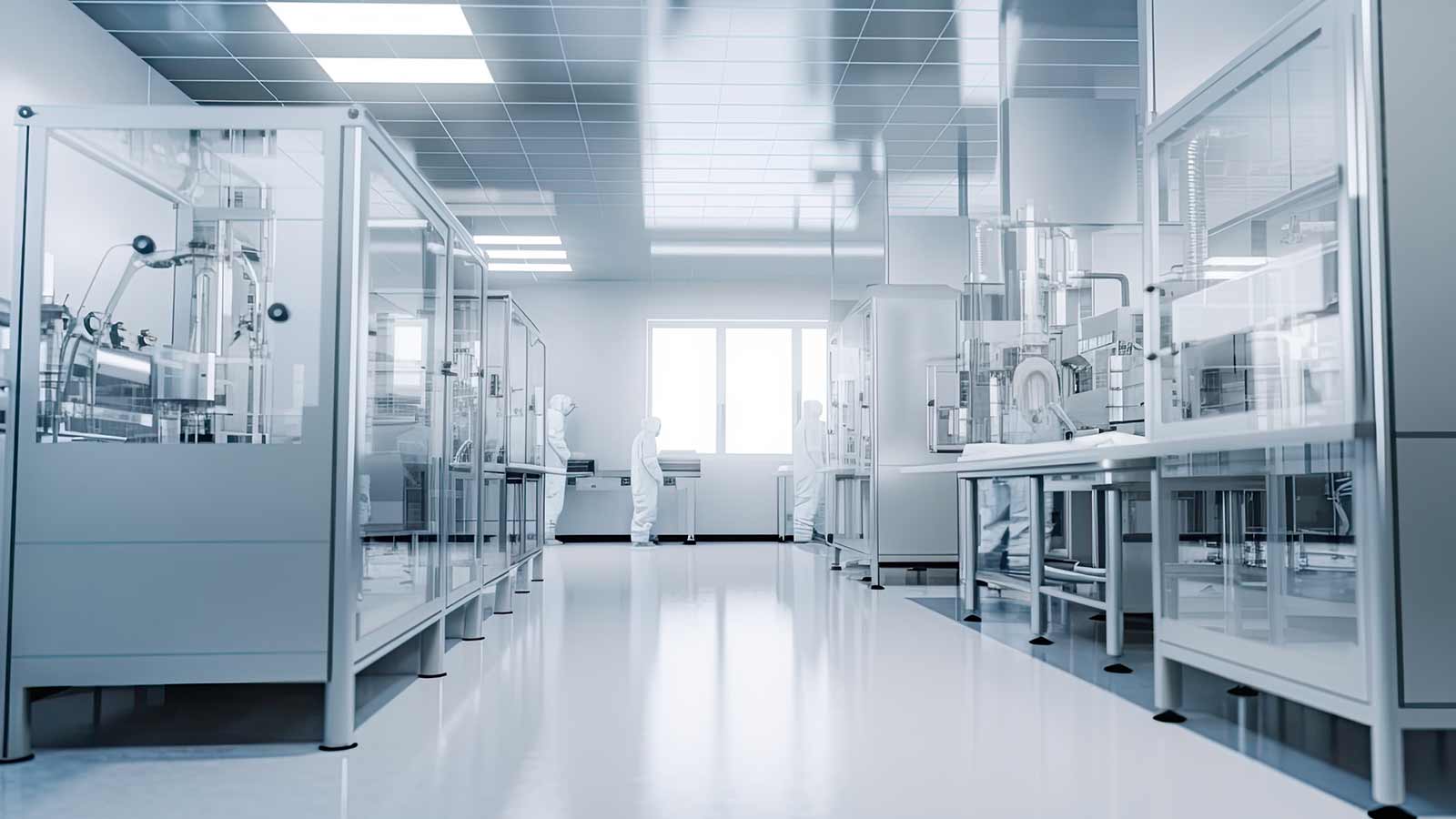
As it is essential to work according to technical cleanliness standards, especially in the automotive industry, a concrete definition of technical cleanliness was developed in the mid-1990s. The VDA (German Association of the Automotive Industry) published a first edition (VDA 19 – Part 1) in 2004 and a second edition or part 2 on this topic in 2010. It contains recommendations and helpful guidelines for planning and quality assurance. The book describes how particle contamination can be prevented and eliminated. The following factors have an immense influence on the technical cleanliness of components:
- Planning, joining and cleaning processes in companies
- Cleanliness areas and their precise planning
- Packing and unpacking, transport routes and storage of components
- Employee qualification, clothing and internal compliance with basic rules
Dirt brake
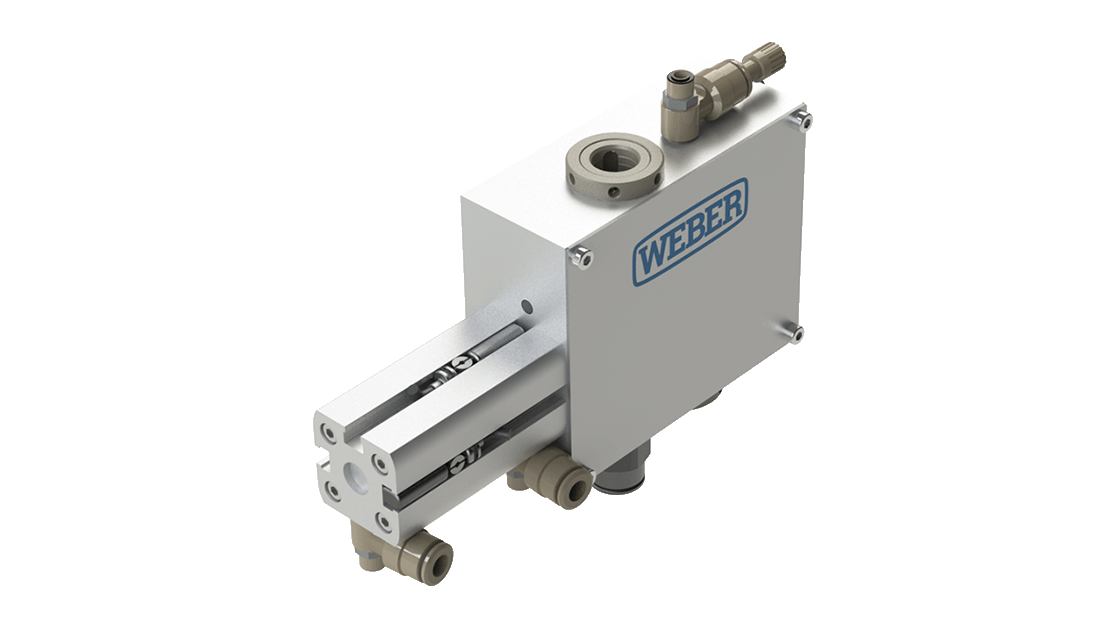
Technical cleanliness is a top priority at WEBER: With our optimized systems, our customers can avoid up to 90 % of metallic dirt particles at the screw location and are therefore in a first-class area of technical cleanliness. Particles and other contaminants are successfully excluded from all our feed processes by means of a dirt brake. Transport air, which may itself be contaminated by particles from the fasteners, is extracted. By using the optional dirt brake, the actual feeding process is not disturbed or slowed down.
Frequently asked questions about technical cleanliness
What does the current VDA-2 from 2010 say?
The German Association of the Automotive Industry (VDA) published the first edition of “VDA 19 Part 1 – Testing technical cleanliness” in 2004. Part 2 “Technical cleanliness in assembly” was published in 2010 and is regarded as the “bible of technical cleanliness”. The driving force behind this was the car manufacturers and suppliers, partly because electronics were increasingly being installed in cars worldwide from 1995 onwards. It contains recommendations and guidelines for quality assurance planning. Detailed instructions describe how to prevent contamination by particles with a size of 50 – 1,000 µm. They also describe how particles can be separated out and how production parts can be protected from contamination
For which components and application areas is technical cleanliness particularly important?
Technical cleanliness is especially crucial for all electrical and metallic components. Even the slightest particle contaminations can have serious consequences such as short circuits, leading to recalls. Especially in the automotive industry, but also in the electronics industry, technical cleanliness is indispensable in production processes. While in the past, a side mirror functioned without electronics, today it comes with a variety of electrical components: electric adjustment, heating elements, sensors for accident prevention, and camera systems. Technical cleanliness is essential for flawless operations.
About our expert!
WEBER components for technical cleanliness
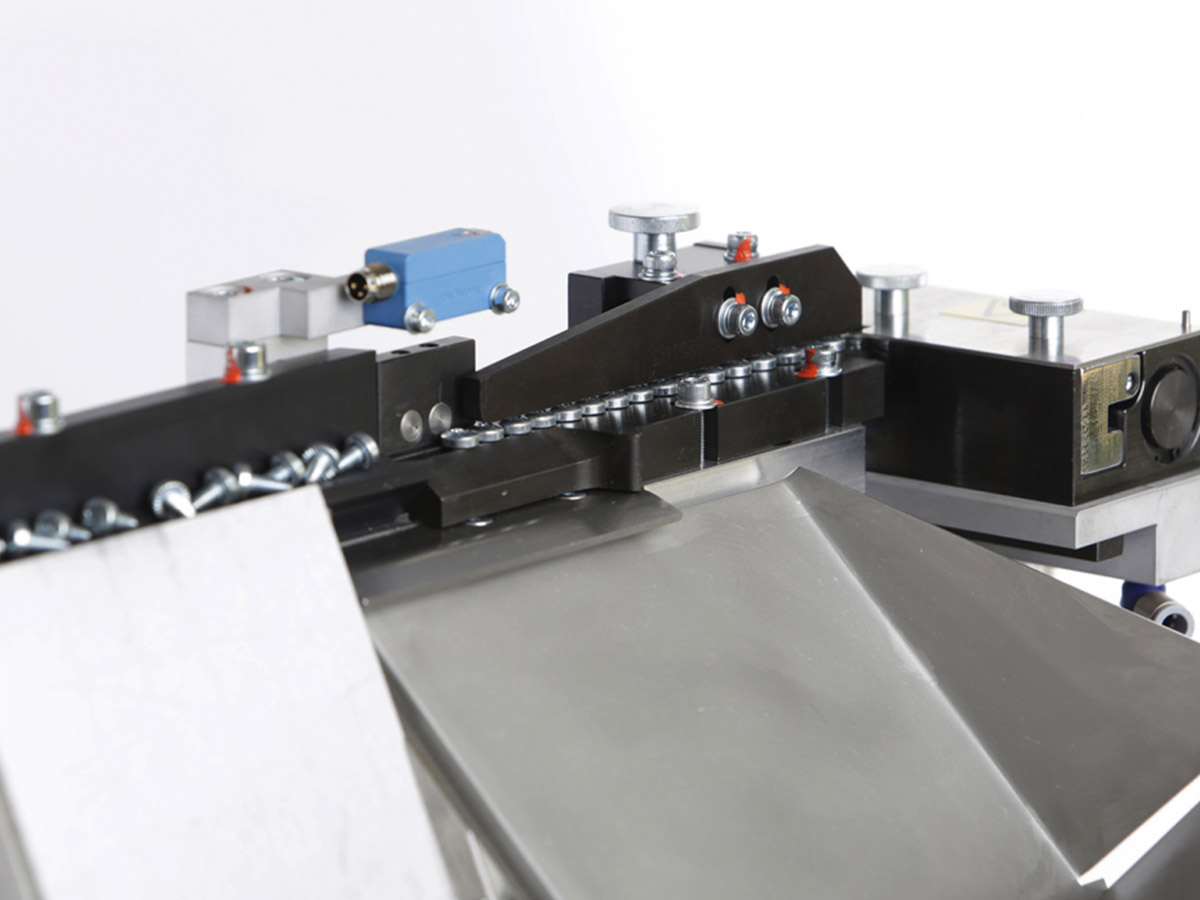
Verbindungselemente zuführen
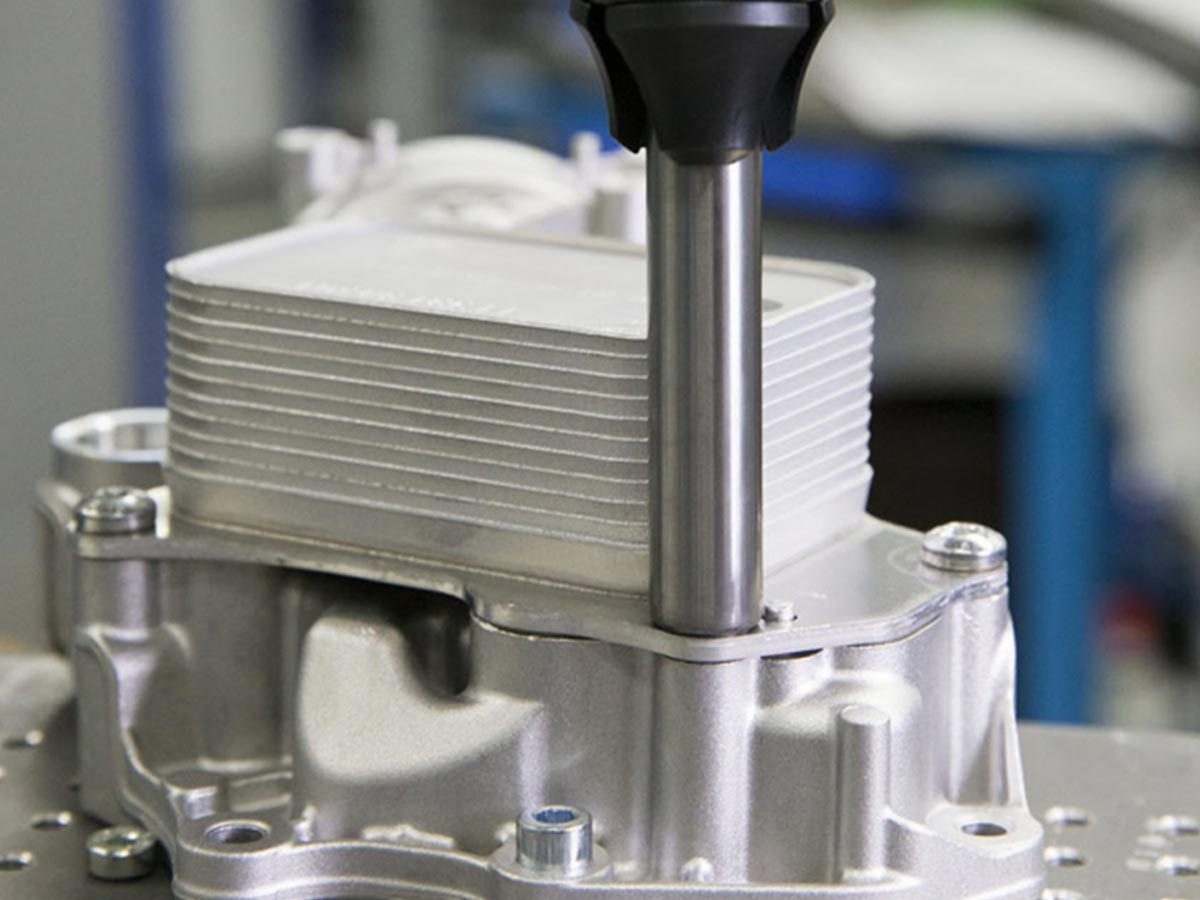
Screwing with vacuum technology
WEBER Schraubautomaten
WEBER Schraubautomaten GmbH is a family-run and innovative company that attaches great importance to the sustainable design of the value chain. The result is high-quality products with maximum process reliability that make production processes more efficient. Your success is our success.