Put simply, automatic feeding is the technical transport of screws (and other parts) from the start position through a tube and into the screwdriver. 2 different variants of feeding systems are available, each with a different approach.With automatic feeding, we achieve maximum process quality. But how exactly does the whole thing work? We show you step by step how automatic separation works.
How automated feeding works
What automatic feeding means
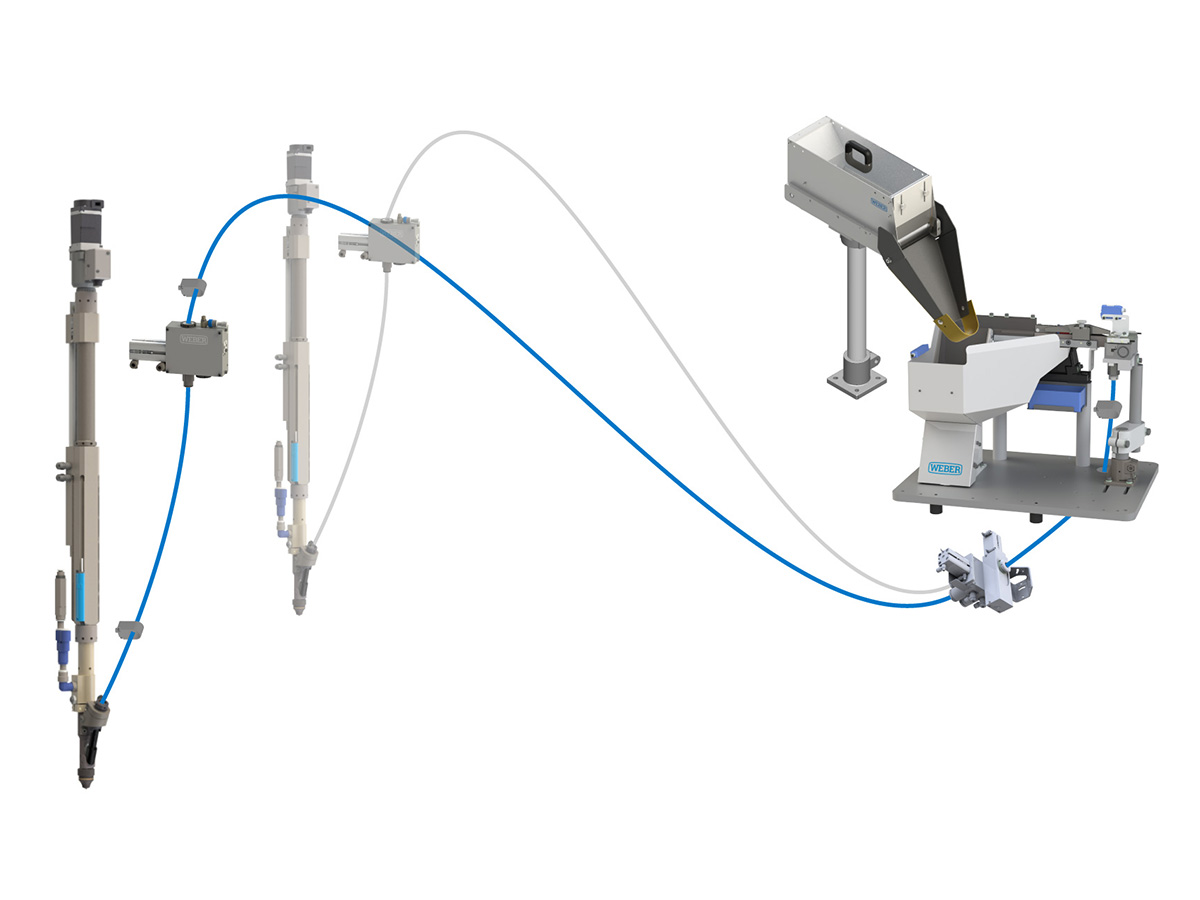
Function principle of automated feeding systems
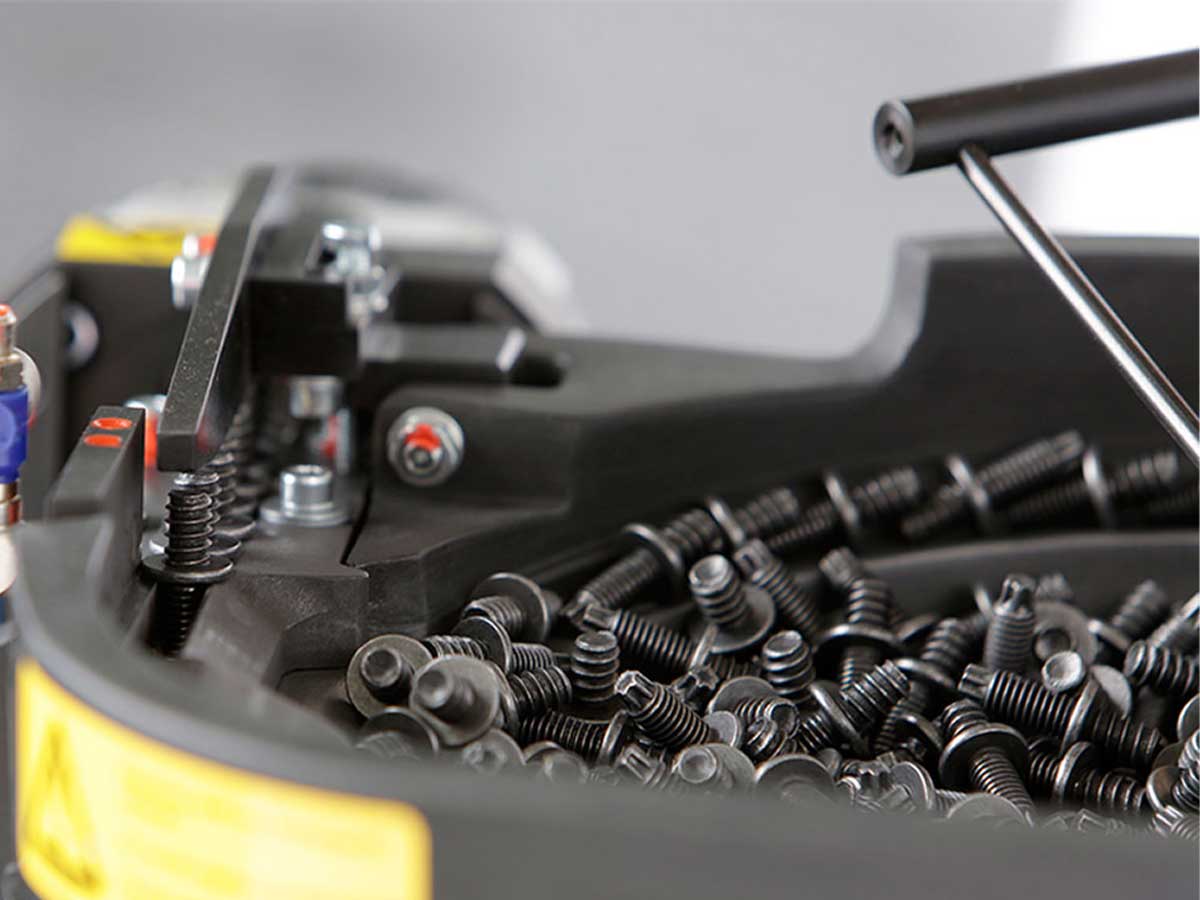
The parts to be transported are initially stored in a bowl. They are then sorted into the correct orientation and separated. An air flow that was previously correctly adjusted to the respective parts ensures that they are blown into the hose with the correct speed. In the following, we show you the process of automated feeding step by step.
These parts are separated and fed
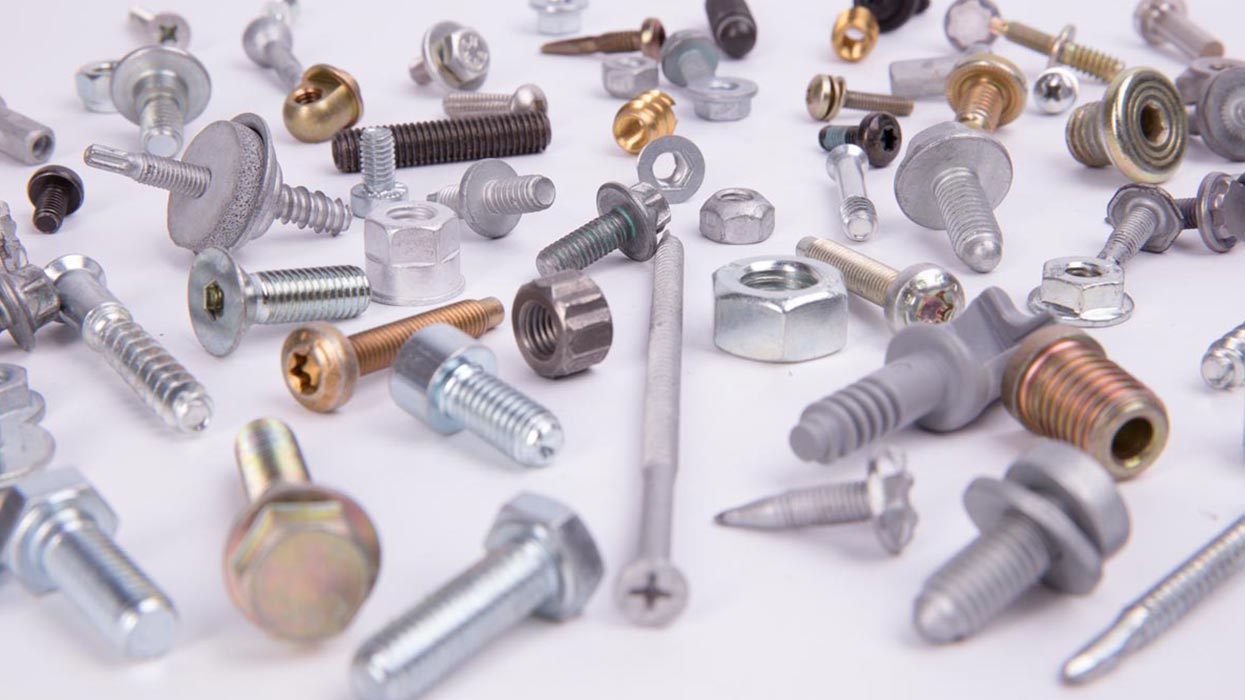
Only screws are fed with an automated feeding system. Correct? Not quite. The following parts can be transported in addition to screws:
nuts, set screws, washers, caps and many other elements.
The fasteners to be fed are usually made of metal or plastic and have a diameter of up to 32 mm with M16 format (M = metric thread) and a length of up to 160 mm. Special purpose parts can have a diameter of up to 32 mm.
2 variants of automated feeding
ZEL step feeder
In the linear feed unit, the screws move towards the separation in a perfectly straight line. The advantages of this variant are gentle handling of the parts, a low noise level and technical cleanliness. The screws and nuts are shaken about less in this system.
ZEB bowl feeder
With this variant, all parts are placed in a sorting bowl. Vibrations are used to transport the parts upwards in the bowl in a spiral motion and moved into the correct position by sorting. While this process shakes the parts about a little more, it is usually more cost effective and has a higher throughput.
Accessories
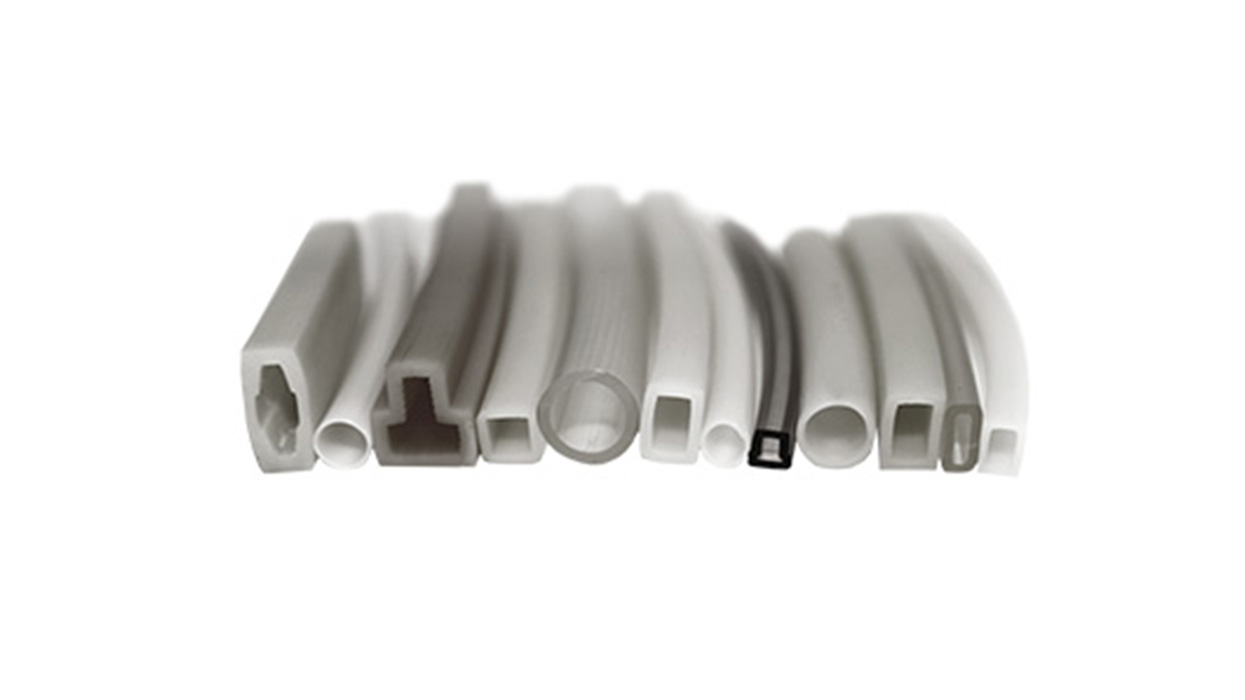
Feed hose
The hose is a key component of the automated feeding system – screws, nuts, washers, set screws and caps are “shot” through at a speed of up to 10 m/s. The clock rate for screws, set screws and nuts is up to 0.8 s per element.
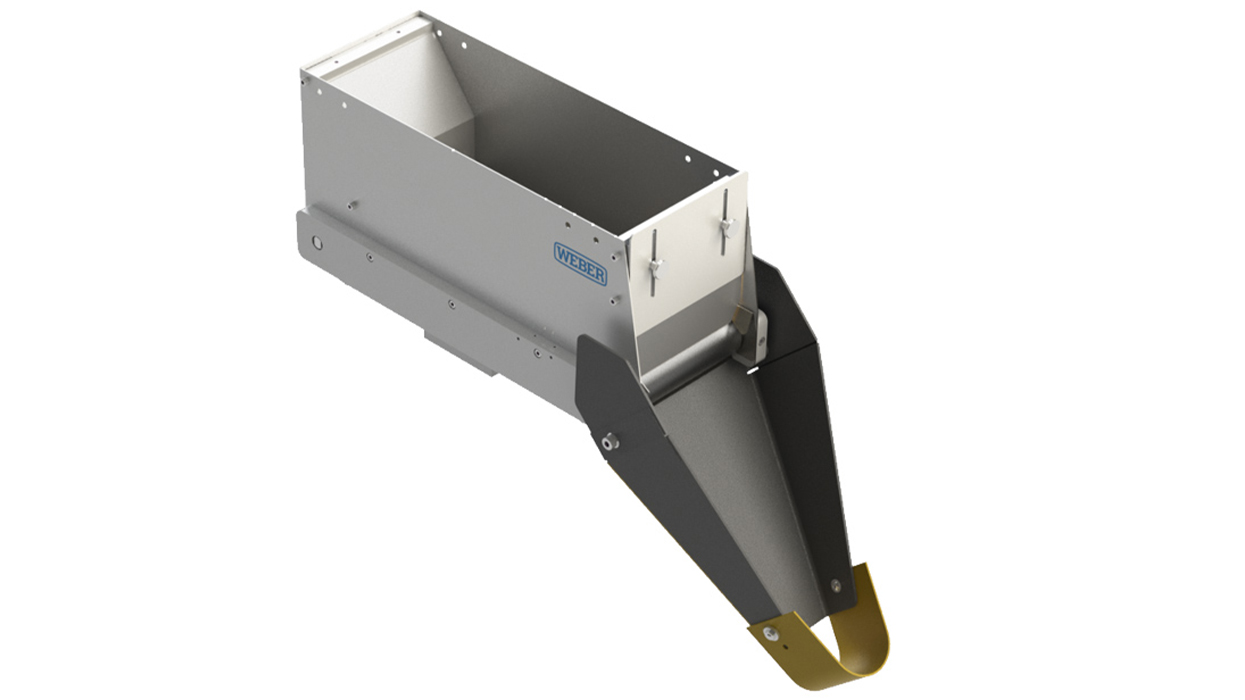
Belt hopper
All required parts are filled into a large belt hopper. Once the small container of the feeding system is empty, it is refilled with the pre-defined quantity from the belt hopper. The belt hopper extends the autonomy of the feed unit until the next filling.
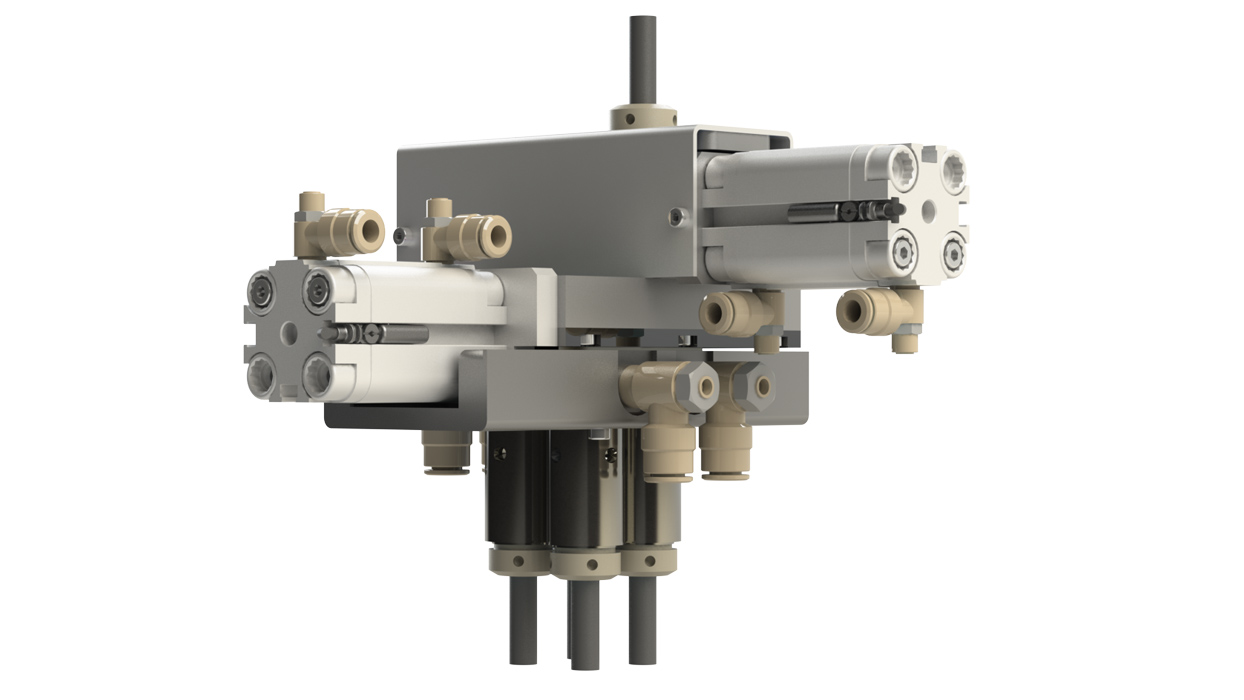
Distributor
If the feed unit supplies more than one screwdriver, a distributor is required. A sensor installed on the hose detects in advance when the corresponding part arrives at the distributor. The distributor then actuates the respective screwdriver or spindle. Imagine the separator as a set of points for train tracks to guide the train in the desired direction.
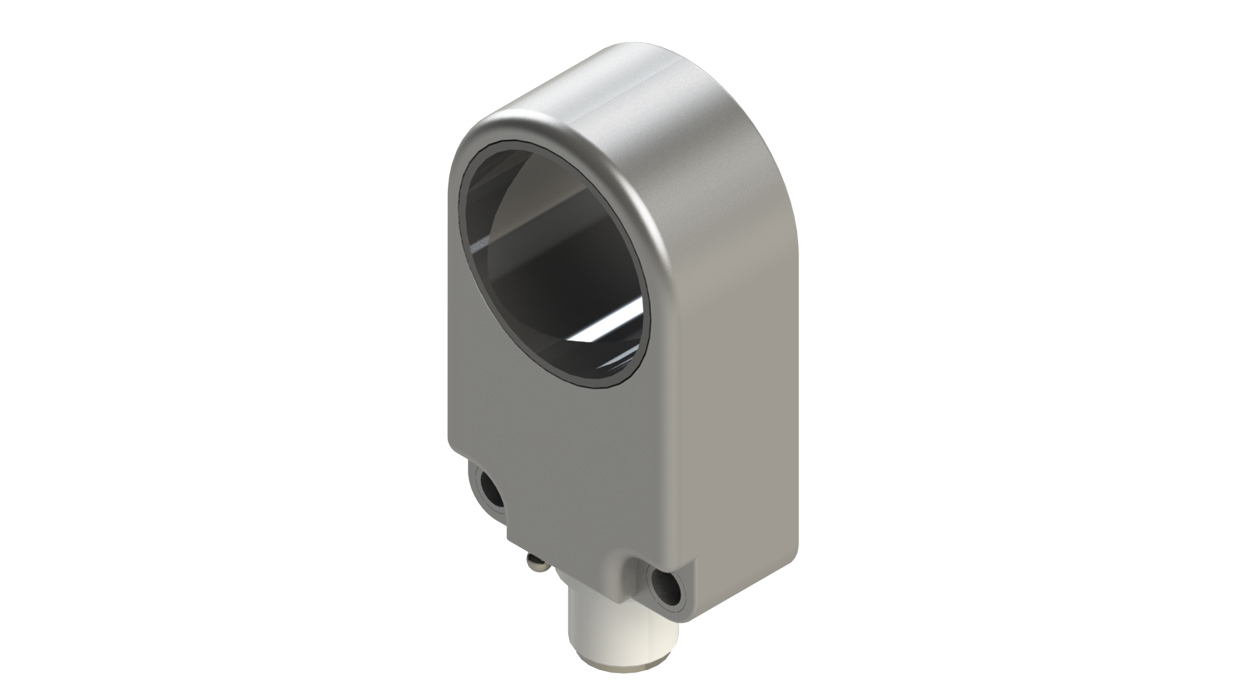
Ring sensor
Ring sensors installed directly on the hose detect at which position the screw is in the hose. They also automate the time when the next screw has to be injected
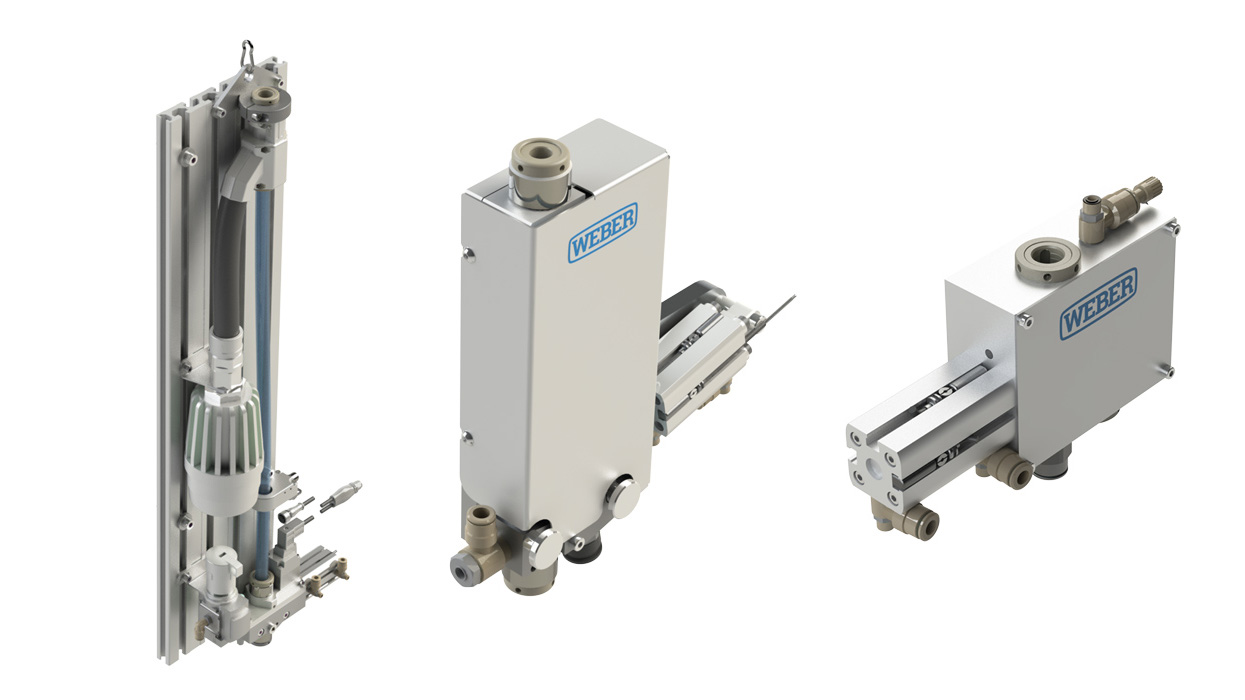
Brake
A brake at the end of the hose initially holds back the screw. The injected parts arrive at high speed and first have to be held back just before the spindle so they can drop into the screwdriver “gently”. Safety first: If heavy parts were to drop into the spindle at full speed at the end of the hose, this could cause damage to the equipment in the worst case.
Technical cleanliness
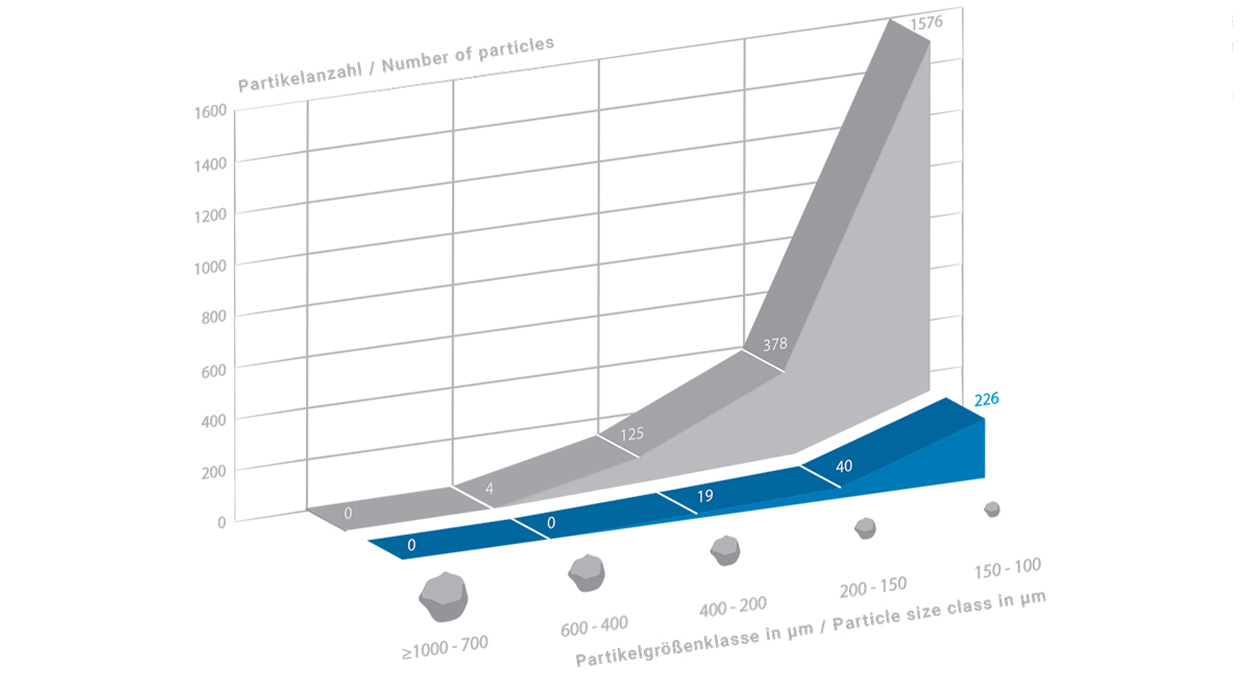
A vacuum process used for the automated feeding system ensures technical cleanliness. A filter extracts and collects industrial dirt on the brake. Step feeders in particular offer the advantage of low-noise, gentle transport of fasteners
Conclusion
Automatic feeding systems use a complex process that can be implemented in different variants. We are always working on improving our process quality and are always available for questions on automated feeding systems. https://www.weber-online.com/en/feeding-systems/
Contact our expert.
Mr. Hofmann has been working as a product manager specializing in feeding technology for 3 years. His career at WEBER Schraubautomaten GmbH began 34 years ago with an apprenticeship as an industrial mechanic. After gaining a master’s degree in mechanical engineering and becoming head of the feeding technology department, he deepened his specialist knowledge in the design and development department of companies in similar sectors.
FAQ ON AUTOMATED FEEDING SYSTEMS
Can different screw variants be used in the same feeding system?
Yes. It is possible to process different screw sizes and formats in the same feeding system. If you have any further questions about special sizes and formats, please contact us. Suitable products can be found at https://www.weber-online.com/en/feeding-systems/
How many screwdrivers can a single distributor supply?
One distributor can typically supply up to 4 screwdrivers. In special cases, it is also possible to actuate more screwdrivers.
What is a PLC?
PLC means “programmable logic control”. A digitally programmed device is used to control a machine or system. The PLC works on the basis of input and output signals.
Where are feeding systems used?
Feeding systems are found primarily in the automotive, timber, electrical and pharmaceutical industries.
WEBER Schraubautomaten
WEBER Schraubautomaten GmbH is a family-run and innovative company that attaches great importance to the sustainable design of the value chain. The result is high-quality products with maximum process reliability that make production processes more efficient. Your success is our success.