Wolfratshausen – On 4 July the attention of the technical world turns to Shanghai where for four days the industry will meet at the Automotive Manufacturing Technology & Material Show (AMTS). For WEBER this is a must-attend event and reason enough to celebrate the world première of the fourth generation of its RSF25 flow drilling screwdriving spindle in front of an international trade audience in China. The WEBER RSF25 answers many questions that the modern manufacturing industry is asking: How can screw connections be implemented with greater flexibility, intelligence, speed and precision than ever before? The RSF25 is nothing less than the answer to all these questions – and it also opens up additional development potential for the next few years. To sum up: The RSF25 embodies the future of modern manufacturing! In the development process of the new system WEBER took a completely new approach. The future-oriented RSF25 model was created through direct and continuous exchanges with relevant customers in order that their frequent requests for considerable increases in efficiency, further quality optimization and significant cost reductions could be taken into account early in the planning phases and then flow into the actual development. “WEBER have incorporated more than 20 years’ experience and know-how into the RSF25, which once again defines the standard for process safety, flexibility and thereby efficiency and cost optimization in automatic screwdriving processes,” explains a happy Dirk Winter, sales manager at WEBER. And one more thing: “We already have over 1,000 flow drilling screwdriving systems in use worldwide. This screwdriving process that was largely jointly-developed by our company has a bright future ahead of it – and WEBER has been setting the pace internationally since the introduction of this technology. However, the RSF25 was only developed for one purpose, namely to better fulfill the requests and requirements of our customers for maximum flexibility and optimum efficiency. The ultimate result of an investment in automation should be higher profitability.”
WEBER presents the fourth generation of its automatic flow drill screwdriver
WEBER is a world market leader for machines and systems for the automation of screwdriving and joining processes and is now enabling maximum efficiency and consistently high process quality with its new screwdriving spindle for flow drilling screws
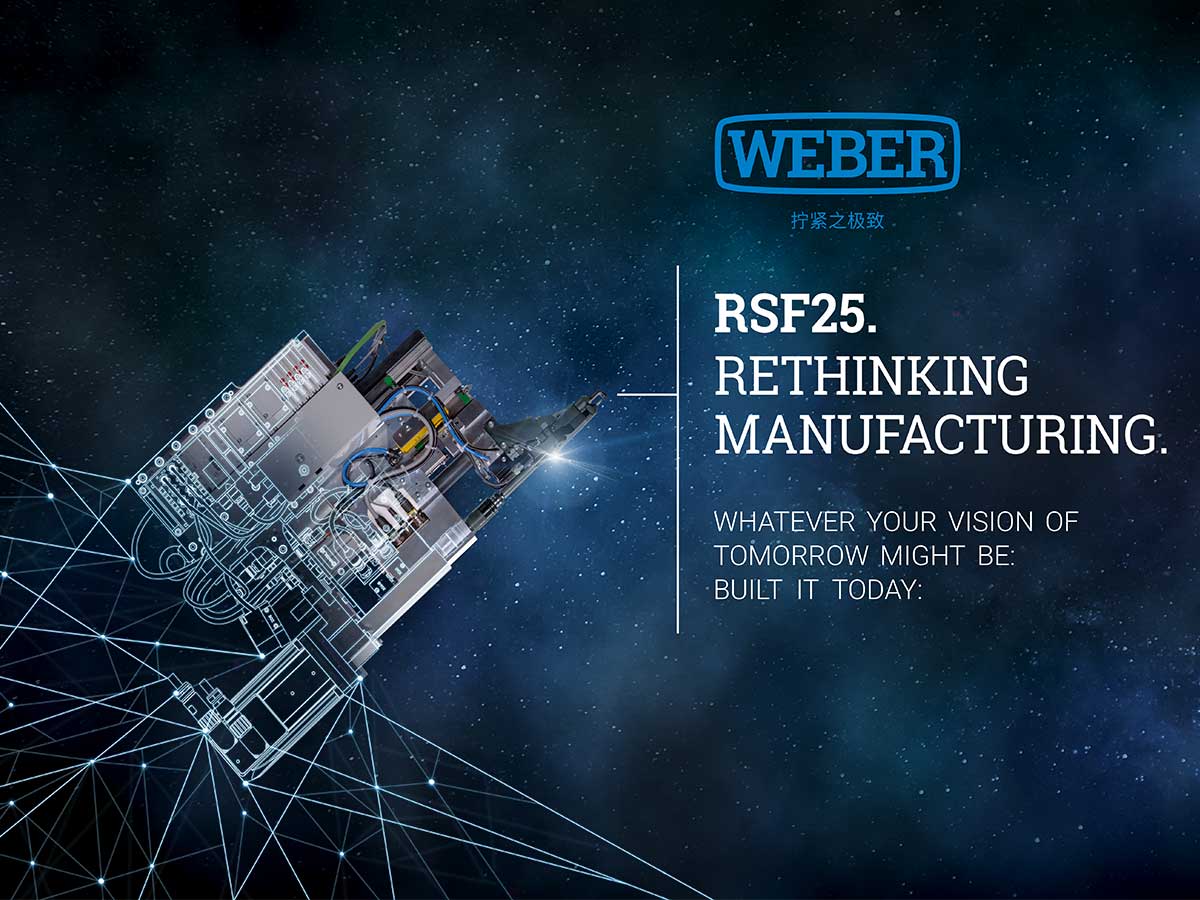
The screwdriving process for lightweight construction
Flow drilling, i.e. self-tapping screw connections, are being used increasingly in profile-intensive lightweight vehicle body construction. These are assembled with special robot-supported screwdriving systems with speeds of up to 8,000 RPM and contact forces of up to 3600 N. In order to ensure that assembly is more consistent and reliable, alongside traditional screwdriving measures (torque, rotation angle), screw depth is used as a control and monitoring value. The screwdriving process using the depth gradient as a control criterion, increases process quality and decreases cycle time. Although steel is still the predominant material in the metal processing industry, use of other specifically lighter materials such as aluminum has increased over the last few years. The optimum utilization of the features of these materials and/or their combined use have caused a rethink in joining technology. And this is where flow drilling screwdriving with the RSF25 comes in. For assembly using this process, an eyelet is created with high RPM and high contact force in which the thread is then formed. After these two steps the screw is conventionally tightened at torque in the area of 10 Nm. The swarf-free metric female thread formed during the screwdriving process is true to gage, which means a standard metric screw can be used for repairs. Through the engagement of several threads free from play, the newly created joint can transmit both high pull-out resistances and high shear loads. The heat generated by the flow drilling process is safe as it is below the recrystalization temperature of the screwdriving materials. However, the residual heat is sufficient to constrict the formed eyelet after assembly onto the screw thread. Since it is not absolutely necessary to prepare the components (pre-drilling, punching), tolerance problems with the hole cover of the clearance hole and threaded bore are avoided. Single-sided accessibility to the component also enables assembly in hollow profiles without a counterholder.
No compromises in process safety
The new RSF25 does not compromise on its focus on process safety and this also includes the documentation of all screwdriving processes. Irrespective of material tolerances and component deformation, the patented WEBER depth gradient process enables control of the screw feed speed (WEBER has a patent on this technology). When the screw tip penetrates the metal, the system registers a surge and then determines the ideal switching point from flow drilling to thread forming mode. The RSF25 is a typical “two-in-one product”: Speed, flexibility and process safety are as inextricably linked for WEBER as short cycle times, ease of use and ergonomics. For the market leader WEBER, all these features always form part of its service provision. This is the only joining process that ensures customers can achieve those particularly innovative screwdriving processes which will characterize assembly processes in the most diverse of sectors today and in the future. And according to Dirk Winter, “The RSF25 honors all our promises to our customers. We have created an intelligent screwdriving system that will contribute to making automated screwdriving and joining processes more effective, more precise and therefore safer for many application areas.”
We are happy to help you!
WEBER Schraubautomaten
WEBER Schraubautomaten GmbH is a family-run and innovative company that attaches great importance to the sustainable design of the value chain. The result is high-quality products with maximum process reliability that make production processes more efficient. Your success is our success.